Honour the past - be the future.
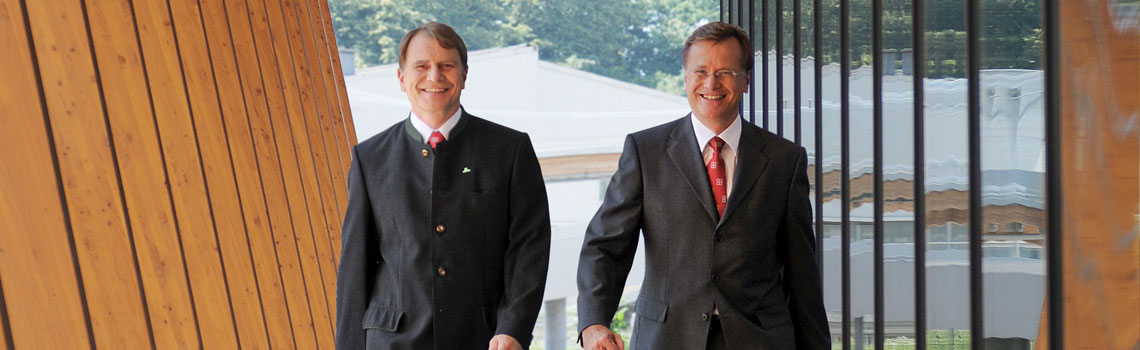
Klaus and Heinz Pöttinger
It is an impressive history that the Pöttinger family and the PÖTTINGER company have written over the past few years. As the Management Team, we are grateful to have been able to accompany a small part of this development in recent years. We are pleased to share responsibility for continuing the success story in the near future.
That is why our top priority is to maintain economic independence and autonomy as a family business.
We look forward to the decades that lie ahead. With this in mind, we continue to work intensively together with our highly trained and motivated employees to offer the best solutions for the challenges that face our customers.
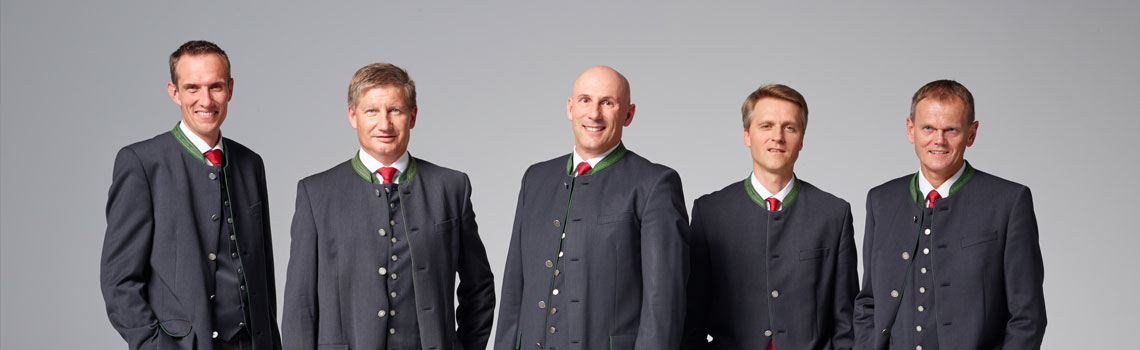
The PÖTTINGER Management team
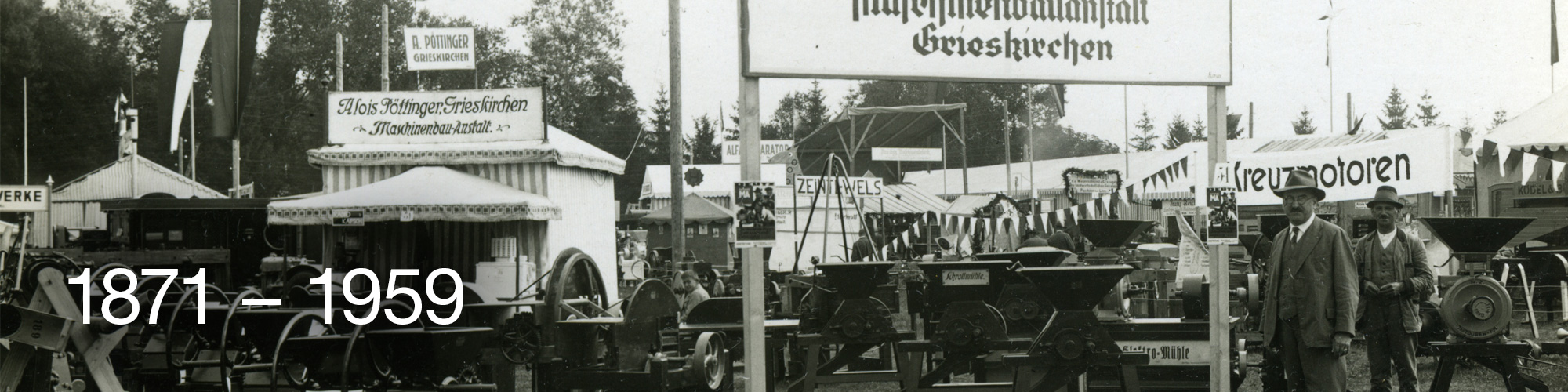
1871-1959
Great, but small: Grieskirchen in Austria was a small town with just over 2,300 inhabitants when PÖTTINGER was founded. The 150-year history of the agricultural engineering company began with Franz Pöttinger in 1871 when he built a forage cutting machine. Interestingly enough, however, the company started out as a locksmith's workshop run by the multi-skilled founder. Franz Pöttinger also made a name for himself as a watchmaker. Among other things, he made the Grieskirchen church tower clock, which was in operation for over 100 years. In 2015 the company's apprentices spent thousands of hours restoring the church tower clock and winding mechanism. It is now on display in its former glory in the staff restaurant at the company's headquarters in Grieskirchen.
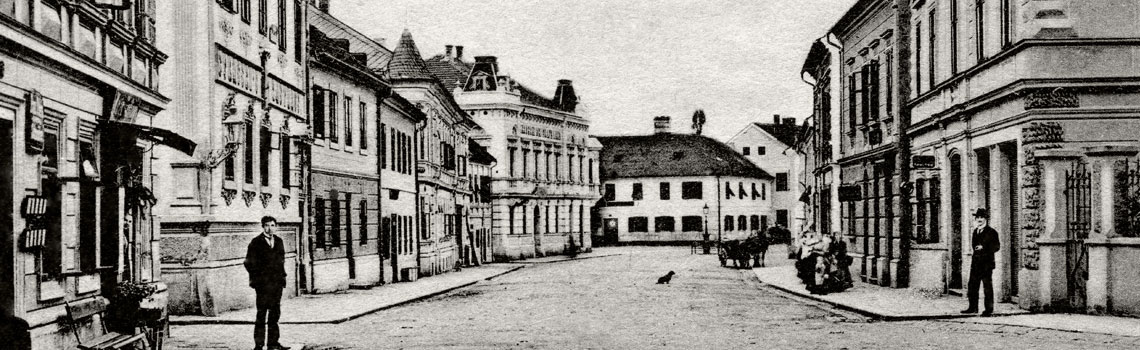
Grieskirchen when the company was founded
The first patent was granted to the busy company founder in 1875 for the forage cutting machine, which saved farmers many hours of manual labour. Franz Pöttinger also invested time and effort in developing other projects: He built water plants and acetylene gas systems for street lighting. This made it possible for Grieskirchen to switch from petroleum to gas lamps.
DThe PÖTTINGER company picked up speed when it was handed over to his son Alois Pöttinger in 1909. The company already employed between eight and ten people. From 1909 the company displayed its first coat of arms with an ear of grain and the initials A and P for Alois Pöttinger. The metalworking business started to evolve into an industrial enterprise, mass-producing fruit mills, fruit presses, malt and flour mills, circular saws, grinders as well as silage and forage cutters.
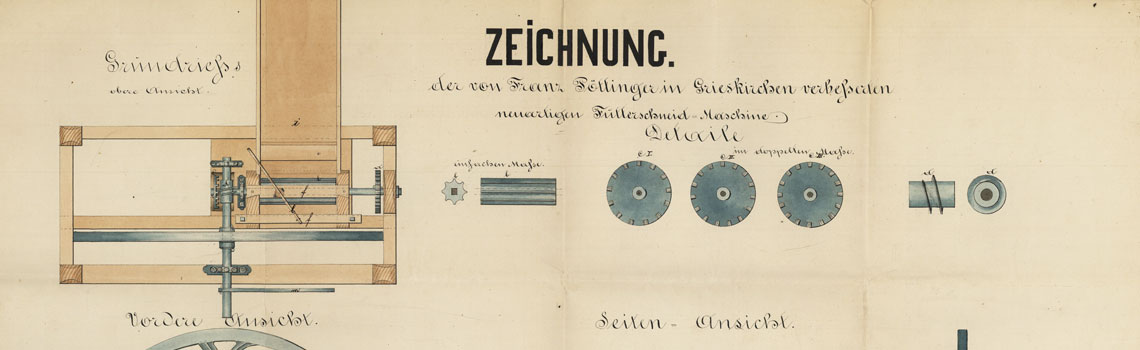
Drawing of the forage cutting machine
In 1920 Alois Pöttinger married and soon their sons Alois, Friedrich (who died at the age of two months), Hans and Heinz followed. During this time the company built their own hydroelectric power station, which made the workshop self-sufficient in terms of energy.
Ever the trendsetter, Pöttinger was the proud owner of the third car to be registered for the road in Upper Austria. In addition to the PÖTTINGER products produced in-house, such as "electric motor wagons for threshing purposes from 6 to 15 hp, with and without motor" and the PÖTTINGER fruit mill, he also carried out a significant development for the region. He installed the water pipes in Grieskirchen as a plumbing company. The plumbing company is still one of the companies within the PÖTTINGER Group in the centre of Grieskirchen.
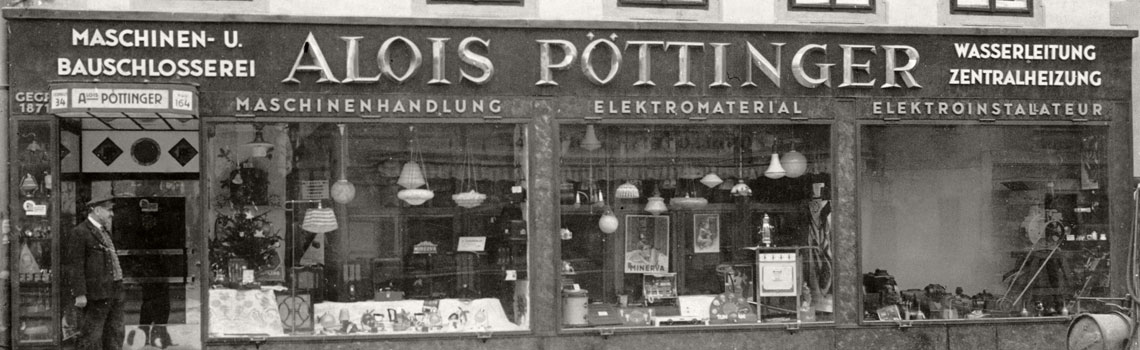
Alois Pöttinger's shop window
In 1938 son Heinz Pöttinger joined his father's company, the "First Grieskirchen Mechanical Engineering Institute," as a mechanical engineering apprentice. His brothers Alois and Hans were already part of the staff and worked as a machine fitter and in electrical equipment sales. In 1939, the father Alois Pöttinger bought an iron foundry from the bankruptcy assets of a machine factory and entered in the company register for the first time as "Alois Pöttinger Machinery Factory and Iron Foundry Grieskirchen". In the post-war years, the company continued manufacturing relentlessly, albeit with a workforce that has been greatly reduced in numbers and machinery that was partly unusable. Gradually the workforce took shape again, some of them refugees and war-disabled. Many of the staff were also part-time farmers. In 1946, the company owner modernised and expanded the foundry, which was overrun with orders. PÖTTINGER started manufacturing fully automatic hydraulic presses. In 1947, the company owner built the first social room for the staff on the roof of the workshop. They also built a new plant for manufacturing swath rakes, which were launched in 1949. Using newly purchased lathes and machine tools, they started production of hay loader wagons in 1951. In the workshops the assembly lines were producing at full tilt.
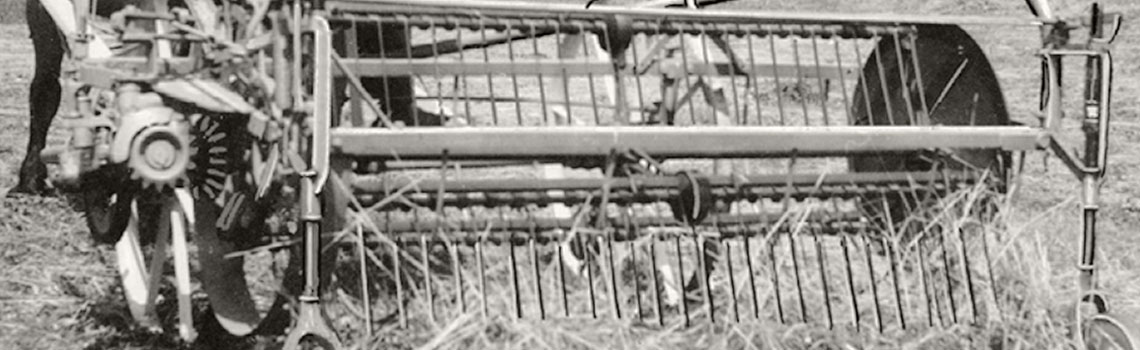
The machine that rakes it in
In the 1950s, the focus of production shifted to agricultural machinery such as hay harvesting equipment, potato harvesters and the new brushwood chipping machines. These machines allowed forestry farmers to process low-grade wood efficiently. The chipping machines were sold through the Bavarian agricultural machinery dealer BayWa - the beginning of a partnership in Southern Germany that has lasted until today. In the 1950s the company did apprentice marketing for the first time: Secondary school pupils from Grieskirchen were regularly invited on tours of the factory.
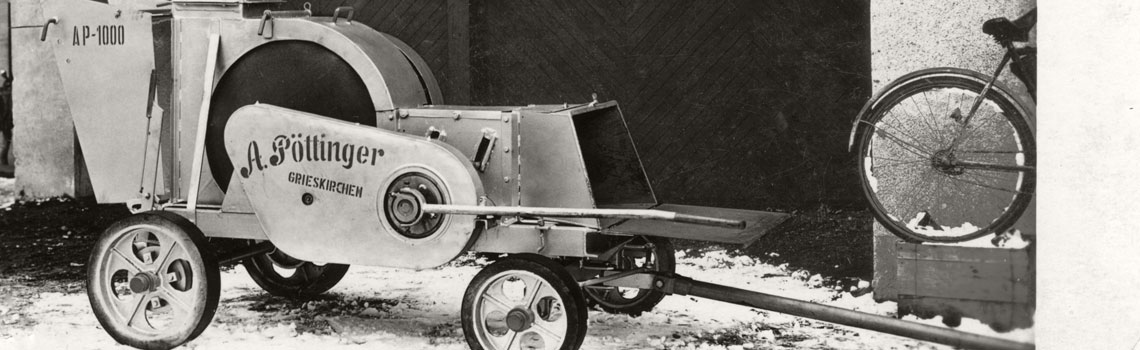
The brushwood chipping machine has advantages for forest work
When Alois Pöttinger senior died in 1958, the management of the company passed to Alois junior, Hans and Heinz Pöttinger. The trio on the executive floor benefited from their different talents in sales, figures and engineering. The series of innovations was therefore continued seamlessly with a loader wagon for "hay, straw, grass, beet leaves and the like". The head of finance, Hans Pöttinger, recorded a total turnover of ATS 19 million (equivalent to approx. EUR 1.4 million), seven percent of which came from exports. This ensured that PÖTTINGER was able to face the 1960s with confidence. Grassland farming was and still is PÖTTINGER's bread and butter core business.
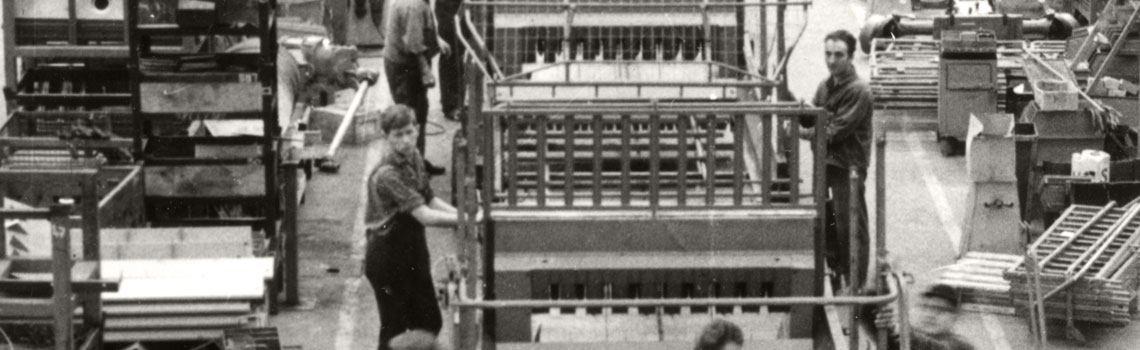
Loader wagon production in the 60s
The fourth generation of the Pöttinger family was not long in coming: Heinz Pöttinger married in 1956 and sons Heinz and Klaus were born soon after, followed by daughters Ulrike and Karin.
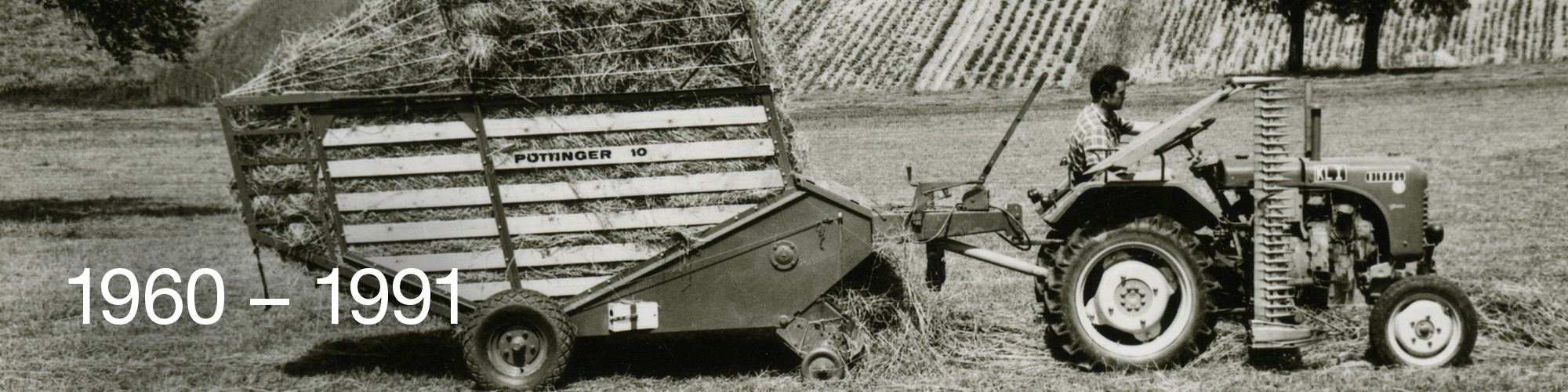
1960-1991
The main workshop in the city centre finally became too small. In 1960, the construction of the new plant began on a greenfield site just outside the city centre of Grieskirchen. From there the company developed to its present size. Six impressive workshops housing assembly lines equipped with the latest machines were completed just in time for the company's 100th anniversary celebration in 1971.
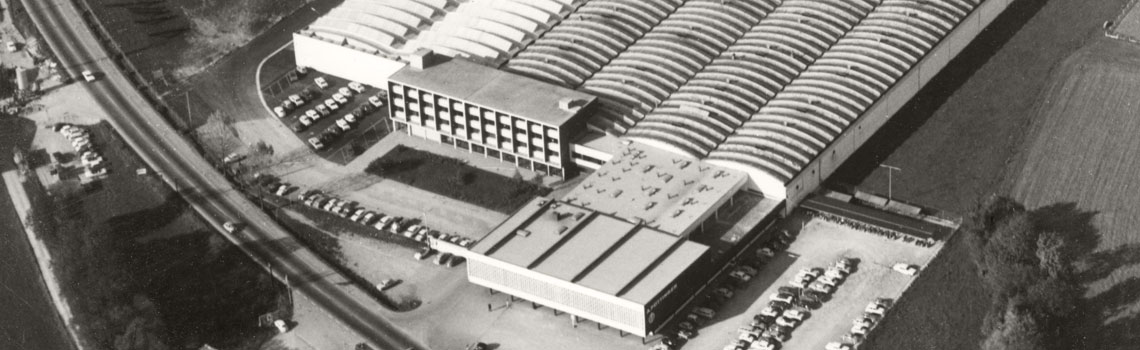
The headquarters at the beginning of the 70s
Around 300 people worked in the agricultural machinery factory. Those who worked at PÖTTINGER were proud of the high technical standards. This positive working atmosphere contributed to the next successful product being created in 1960 - the legendary hay conveyor rake - a self-propelled machine for working on extremely steep terrain.
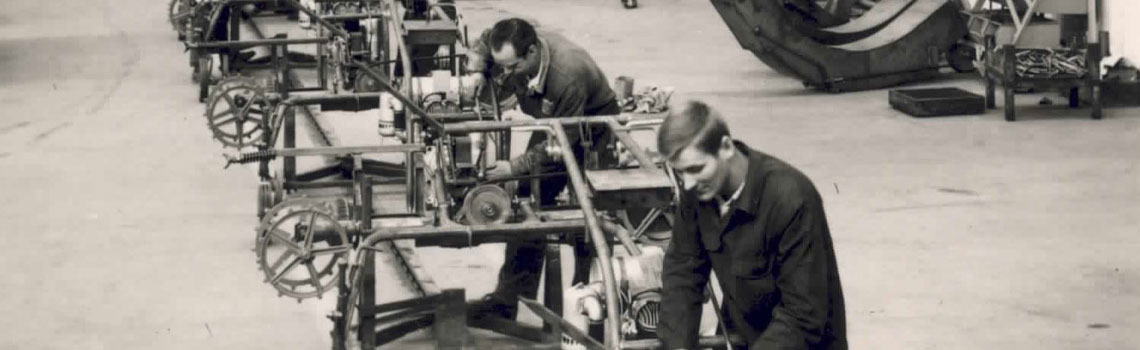
Production of the conveyor rake, which can still be seen in the fields of Austria today.
With the loader wagon for bringing in the harvest, the agricultural engineering company's engineers composed another bestseller in 1963, which has retained its number one position worldwide to this day. In its first year of manufacture PÖTTINGER sold around 1,000 units of the LW14, which was named after its load capacity of 14 m³. The next sales hit perfected a machine that already existed: On the MEX maize forager the cutting drum (standard equipment at the time) was replaced with a flywheel. The company's green product range puts PÖTTINGER on the map as a full-service provider for grassland farming. But even in this segment, the company did not rest on its laurels, and continued to develop new ideas. In 1972, the enterprising company launched the first short chop loader wagon onto the market.
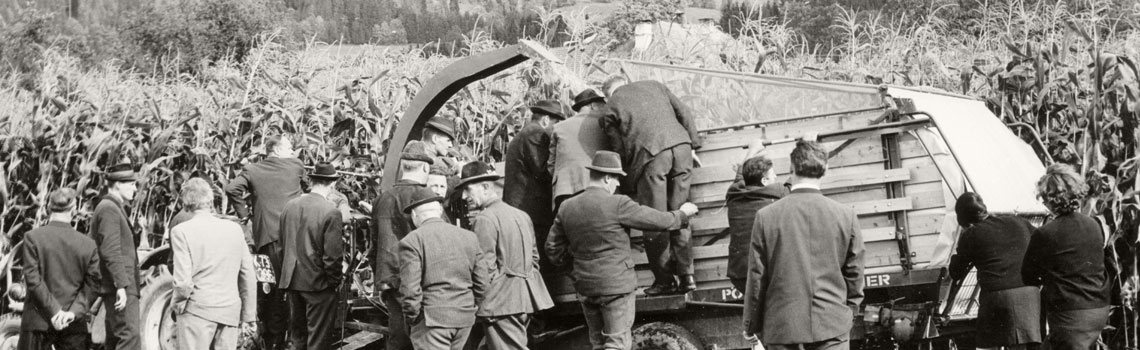
The MEX has a significant impact on the maize harvest.
The company showed an increasing international presence, not just with the service centre set up in Augsburg (GER) in 1964, but also with sales dealerships in various countries and exhibits at major agricultural trade fairs. In 1970 PÖTTINGER had over 800 employees and a turnover in excess of 310 million Schillings (equivalent to EUR 22.5 million), about one third of which was accounted for by exports.
By purchasing the Bavarian Plough Factory in Landsberg am Lech (GER) in 1975, PÖTTINGER was not only prepared for the nearby domestic market but also for the development of a major new business segment: tillage. Although the plough factory had only a modest output, it was a decisive first step for PÖTTINGER into an important segment. 1980 may have been a difficult year, with farmers' incomes stagnated not only in Austria, but PÖTTINGER still pushed ahead with the long-planned modernisation of its product range. The Austrian company is the first agricultural machinery manufacturer to use product names that also work internationally: CAT, HIT, TOP and MEX.
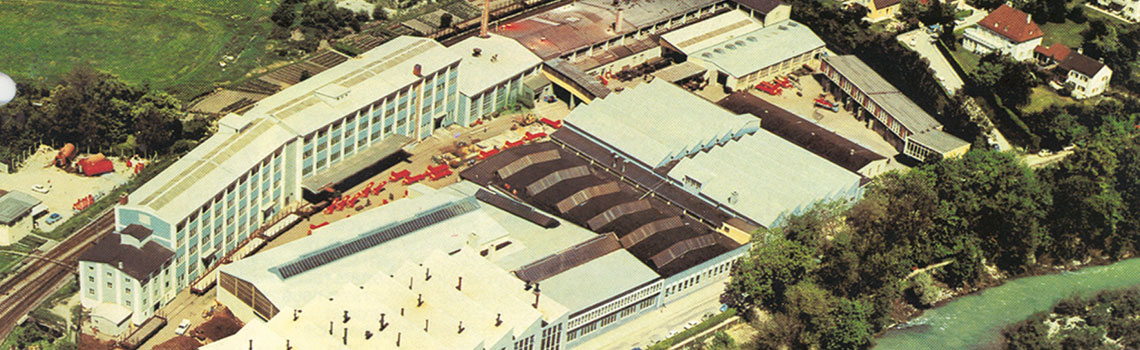
The service centre in Landsberg in the 70s
In the difficult decade of the eighties, the fourth generation officially joined the family business. In 1983/1984, Klaus (who studied mechanical engineering) and Heinz (social and economic sciences) Pöttinger's first task in the company was to get the Bavarian Plough Factory back in shape. The situation in Landsberg improved with the launch of a new and more powerful generation of ploughs. Although built in Bavaria, these heavy-duty tillage implements were marketed under the PÖTTINGER name. The LION power harrow followed in 1991. With the stubble cultivator, the company now had a growing product range for tillage. However, the events at the company were overshadowed by family events: Alois Pöttinger died of heart failure died in 1980. Hans Pöttinger also died of heart failure during a business trip in 1990. As the last of the three brothers, Heinz Pöttinger senior remained at the helm.
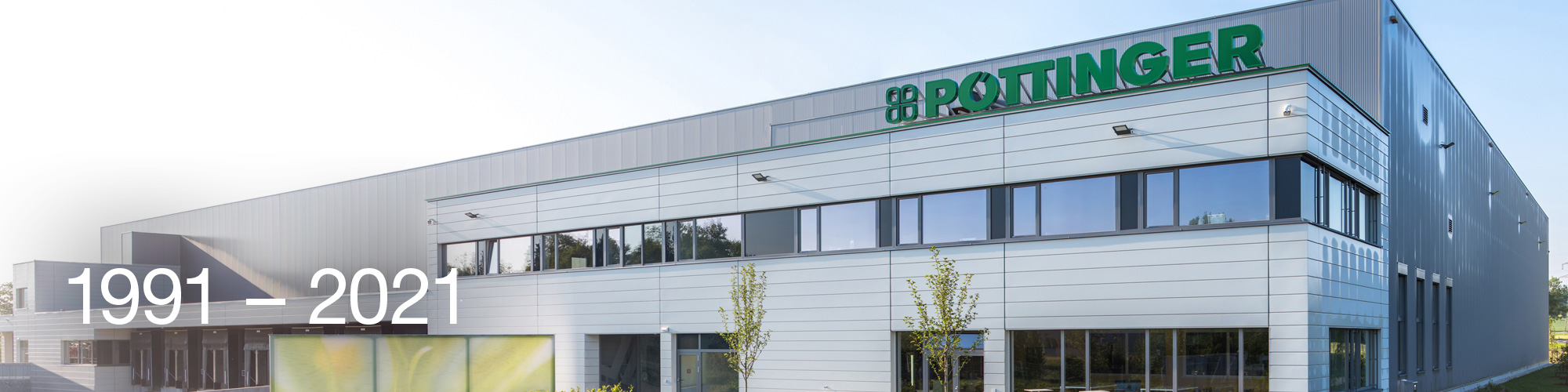
1991 - present
1991 was a year of celebration: PÖTTINGER agricultural machinery company was 120 years old and the Bavarian Plough Factory in Landsberg is 100. On this festive occasion Heinz Pöttinger senior handed over the company to Klaus and Heinz Pöttinger, the fourth generation of the family. Heinz became the head of financial and commercial management and Klaus took responsibility for the technical side as head of engineering.
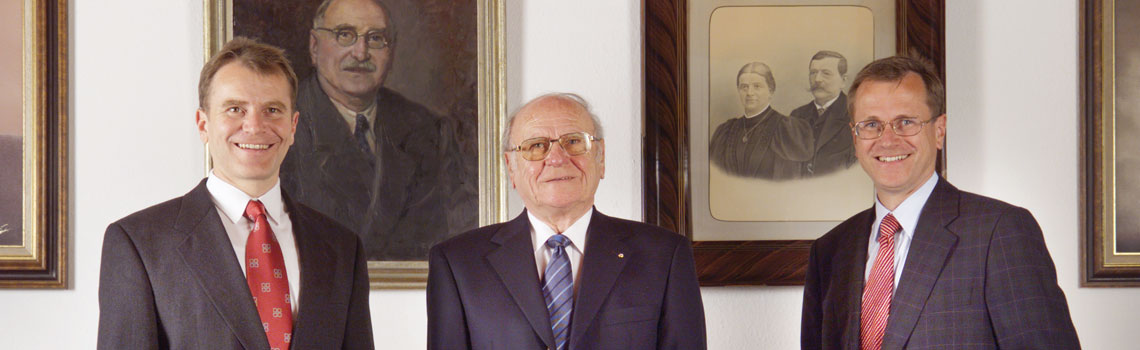
The fourth generation, Heinz and Klaus Pöttinger accept the challenge.
During the first few years they faced enormous challenges. The agricultural machinery market collapsed due to international uncertainty and difficulties with the iron foundry were only the tip of the iceberg. The young business owners were forced to close the foundry and even lay off employees. This was the toughest test for the two young entrepreneurs. The agricultural machinery market recovered again and the decisive steps taken by the PÖTTINGER brothers began to take effect: The number of employees in Grieskirchen was quickly increased again. In order to ensure that the Austrian plant was utilised in full throughout the year, the assembly of ploughs and harrows was relocated from Landsberg to Grieskirchen. The Bavarian factory was reduced to its core competencies: forging basis components.
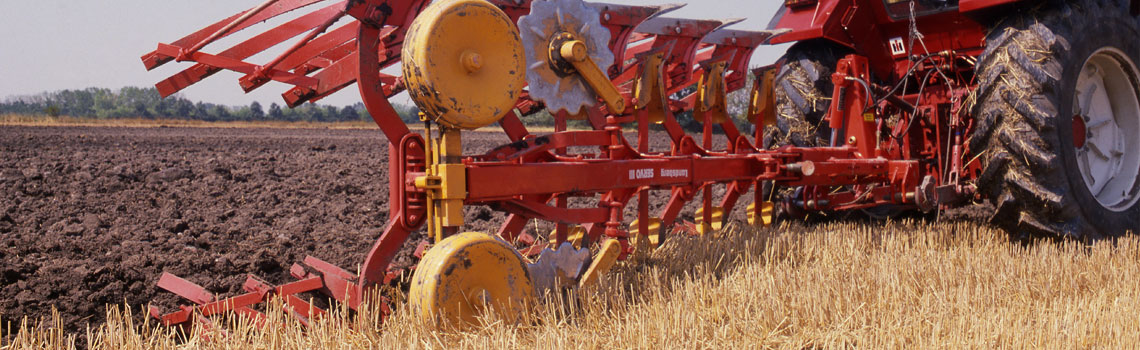
The SERVO was then manufactured back in Grieskirchen.
1993 saw PÖTTINGER venture into the baler market. In the beginning they sold machines made by the German manufacturer Welger. Four years later the company switched to the round balers and wrappers made by Gallignani in Italy. The 1990s heralded the introduction of Kaizen and the improvement process. In 1996, Pöttinger was certified to the ISO 9001 quality management system standard and evolved the existing staff suggestion scheme into the Japanese Kaizen model "Change for the better" in the form of PIP: The PÖTTINGER Improvement Process. Just one year after its introduction, a remarkable 1,000 suggestions for improvement from employees were on the table.
With an investment of ATS 100 million (equivalent to approx. EUR 7.3 million) in the construction of the new painting centre, PÖTTINGER was then able to produce automotive paint quality for agricultural machinery. Shortly before the turn of the millennium, PÖTTINGER really took off in terms of internationalisation. The first sales subsidiary abroad was opened in Alsace, France. By 2021 another 14 sales subsidiary had followed. Around this time, the course was also set for a completely new product line: the company started by investing in 25 percent of the Rabe seed drill plant. In 2001 the time had come for PÖTTINGER to acquire the factory in its entirety and expanded it to become one of the most modern seed drill technology factories in Europe. It featured a completely revised plant layout, laser and powder coating line, additional assembly hall and new manufacturing technologies.
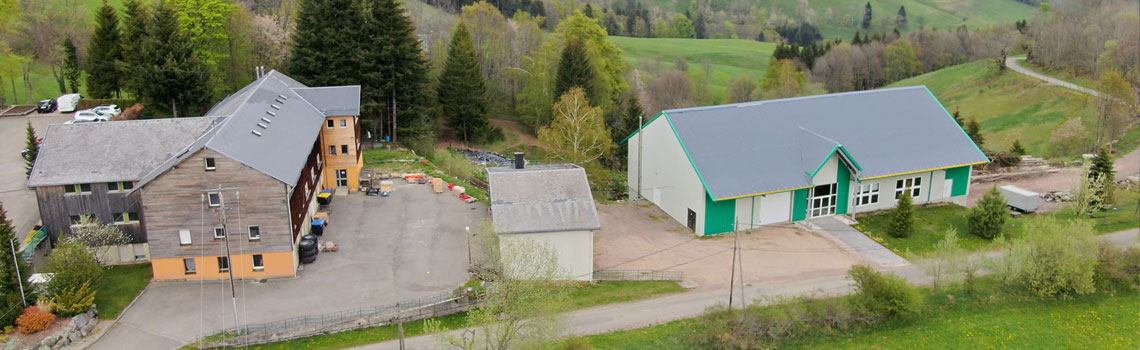
The PÖTTINGER location in France
The early years of the 21st century also saw a new phase of growth. In 2006, the decision was made to expand Vodnany into a development and competence centre for tillage. Since 1995, components for soil cultivation equipment had already been welded in a rented hall in the small Czech town of Vodnany. Following several phases of construction and investment in a gigantic cathodic dip painting line with powder coating and additional manufacturing and logistics halls, the new plant is another strong pillar for the Austrian agricultural machinery manufacturer. Despite its multi-million Euro investments abroad, the company remained true to its roots with numerous investments in the headquarters. In 2008 the new exhibition and customer centre was opened. This includes the company's training centre for providing service training to dealerships.
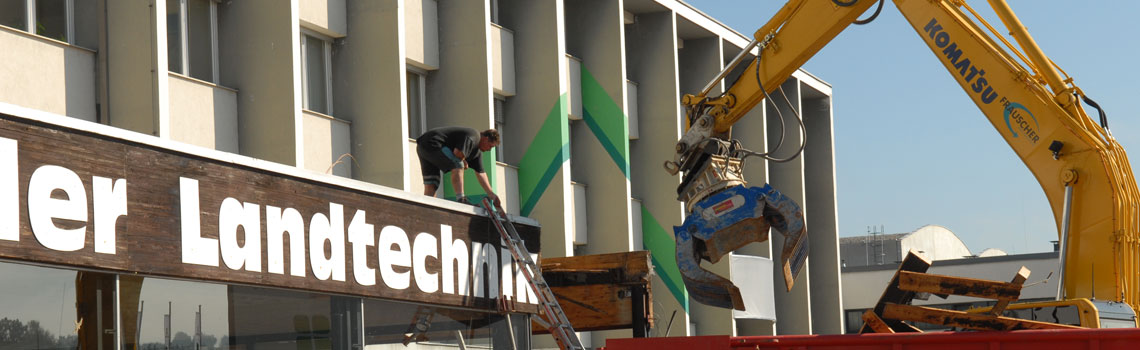
The customer centre under construction at the turn of the millennium.
Research & became an increasingly important department within the company in terms of future projects and testing methods. That is why PÖTTINGER became one of the main shareholders of the TIZ (Technology and Innovation Centre) in Grieskirchen, which opened opposite the company in 2004. In 2014, Heinz Pöttinger passed away. He was the last representative of the third generation. The investments in the company continued in his style: In 2015, the office building in Grieskirchen was renovated and extended. One year later, further investments were made with the construction of two halls for assembly and logistics, and there was the ground-breaking ceremony for the spare parts logistics centre in neighbouring Taufkirchen.
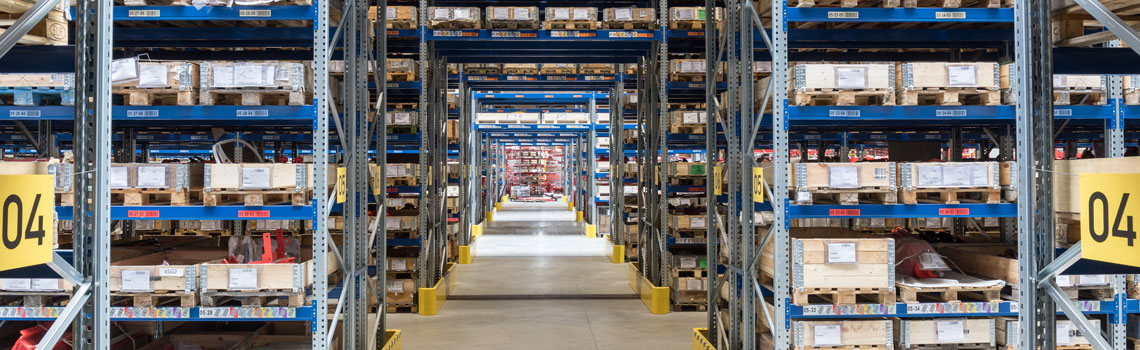
The modern spare parts logistics centre in Taufkirchen, Upper Austria
2015 also saw the start of manufacturing of the company's own balers. The IMPRESS round baler featuring the perfect flow was presented to the farming industry for the first time.
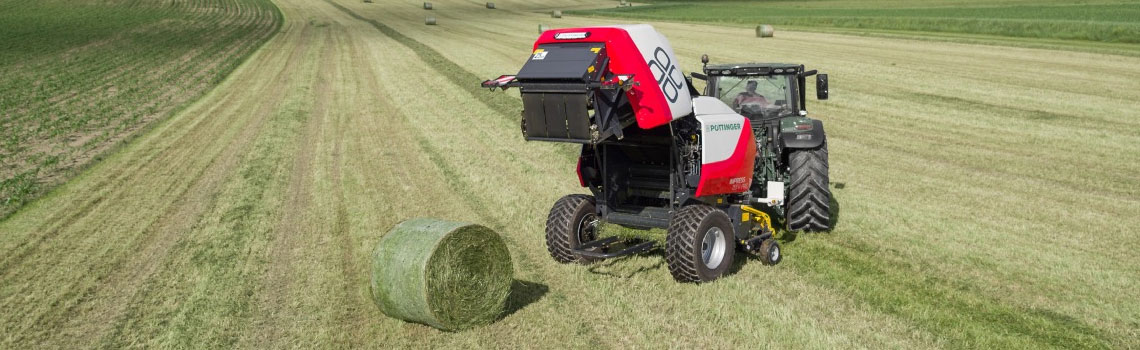
IMPRESS round balers ensure the perfect flow.
Following on from that, there were several changes at management level. After Klaus Pöttinger stood down from operations management in 2016 and Heinz Pöttinger moved to the supervisory board in 2018, a five-person management team from the company's own workforce took over. Gregor Dietachmayr (Spokesperson for the management team and responsible for Sales, Marketing, Service), Dr. Markus Baldinger (Research, Development, Digitisation), Jörg Lechner (Production, Materials Management), Herbert Wagner (Human Resources, IT), Wolfgang Moser (Finance, Corporate Quality).
At the end of April 2020, the ground-breaking ceremony took place for a new plant in the neighbouring community of St. Georgen for manufacturing round balers and large rakes.
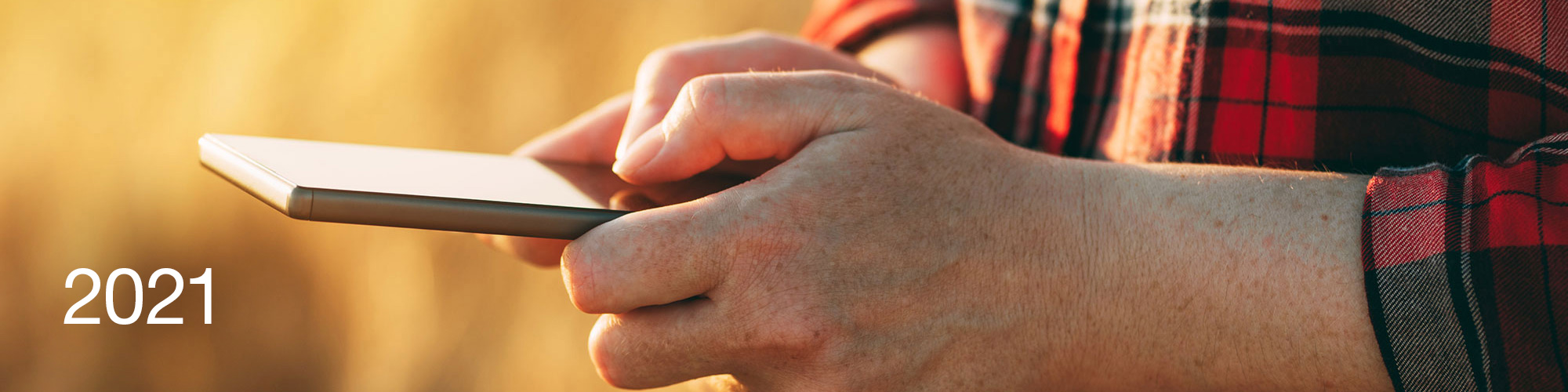
We need to address major challenges - climate change in particular, as well as effectively utilising digitisation and artificial intelligence and coping with a pandemic. The future of agriculture is directly linked to these factors, because everyone needs agriculture. This is the tagline that has accompanied PÖTTINGER's work for many years in boosting the recognition and appreciation of farming. Digitisation and technical progress have long driven the agricultural sector. If the current trends hold, fewer and fewer farm businesses will have to farm more and more and larger fields.
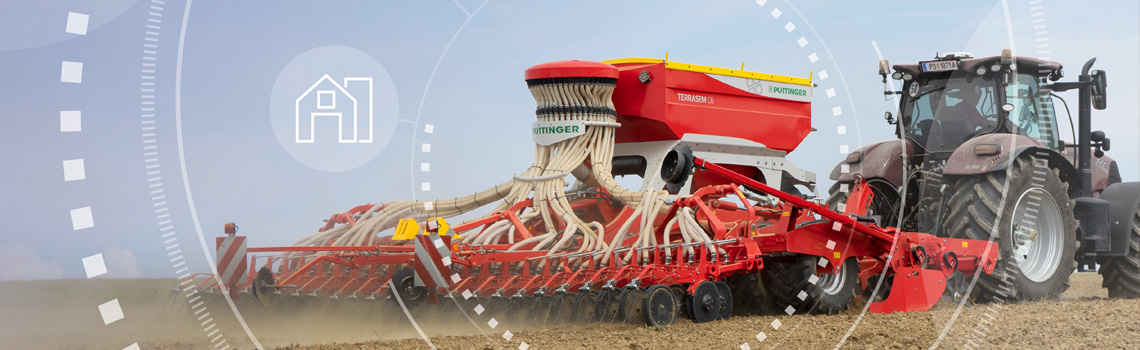
Digitisation
This is only possible with autonomous agricultural machinery, which take account of climate change and by using electrification and working methods that conserve the crops and soil draw as little water as possible from the ground. In keeping with the PÖTTINGER spirit, work on the future at the company has long since begun. With 150 years of technical and entrepreneurial experience, PÖTTINGER is ideally equipped to take on the many major challenges presented by the future. "Honour the past - be the future." is also the tagline of the fifth generation. They look back on the past with gratitude and is on the start line for a successful future.
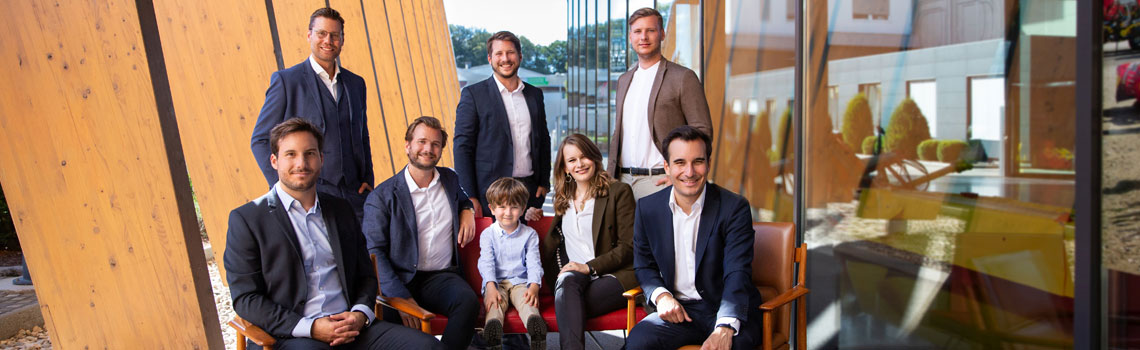
The fifth generation of the Pöttinger family